John Deere 1745 Compact Planter
Drawn Planters
Your Preferred Location
Features
-
Spacing (inches): 15, 30
-
Transport Width: 12 ft. 2 in.
-
Number of Rows: 8, 15
-
Central Commodity System (CCS): N/A
-
Row Unit: MaxEmerge 5
Specifications
Additional Information - Date collected: |
1/7/2020 |
Additional Information - Recommended tractor horsepower: |
71 kW (95 hp) Drawbar. No fertilizer system. 78 kW (105 hp) Drawbar. With frame mounted fertilizer openers. |
Additional Information - Recommended tractor hydraulics: |
See compatibility story. |
Additional Information - Warranty length: |
Standard |
Ag Management Solutions - Field documentation: |
Yes |
Ag Management Solutions - Map-based seeding: |
No |
Ag Management Solutions - Parallel tracking: |
Yes |
Closing System - Cast iron closing system: |
Wheel 2 Position 4 slots Adjustment In-line or staggered |
Closing System - Rubber tire closing system: |
Wheel 2 Position 4 slots Adjustment T handle Down force Spring Alignment In-line or staggered |
Dimensions - Field operation width: |
6.27 m (20 ft, 7 in.) |
Dimensions - Transport height: |
3.84 m (12 ft, 7 in.) |
Dimensions - Transport length: |
8.00 m (26 ft, 3 in.) |
Dimensions - Transport weight: |
Empty with 3 bu. hoppers, no fertilizer system: 5,546 kg (12,227 lbs) Liquid fertilizer with frame mounted openers weight empty: 781 kg (1,722 lbs) Liquid fertilizer with in-furrow weight empty: 425 kg (937 lbs) Dry fertilizer with frame mounted openers weight empty: 1,000 kg (2,205 lbs) |
Dimensions - Transport width (with markers): |
3.71 m (12 ft, 2 in.) |
Dimensions - Transport width (without markers): |
3.71 m (12 ft, 2 in.) |
Drive System - Base: |
Ground drive |
Drive System - Drive wheel disconnect: |
When planter is raised |
Drive System - Number of drive wheels: |
1 |
Fertilizer - Dry fertilizer: |
Number of hoppers 2-Onboard Hopper capacity 1,200 L (42.4 cu ft) |
Fertilizer - Fertilizer opener type: |
Frame-mounted Yes |
Fertilizer - Fixed-rate application: |
Yes |
Fertilizer - Onboard / towed / tractor tanks: |
2-Onboard |
Fertilizer - Pump rate: |
22.4-352 L/ha (2.4-37.6 gal/ac.) |
Fertilizer - Pump type: |
Ground drive piston pump |
Fertilizer - Tank capacity: |
1,136 L (300 gal) total |
Frame - Flexibility: |
Rigid |
Frame - Fold configuration: |
Pivot fold |
Frame - Fold-and-go from tractor cab: |
Yes |
Frame - Frame tube size: |
17.8 cm x 17.8 cm (7 in. x 7 in.) |
Herbicide and Insecticide - Insecticide only hopper: |
Yes |
Hitch - Base: |
Clevis drawbar |
Hitch - Optional: |
Ring style drawbar |
Hitch - Rear hitch: |
No |
Key Specs - Frame - Flexibility: |
Rigid |
Key Specs - Frame - Fold configuration: |
Pivot fold |
Key Specs - Number of rows: |
8 |
Key Specs - Row spacing: |
76.2 cm (30 in.) |
Key Specs - Row unit seed hoppers: |
Capacity Mini, 56 L (1.6 bu), 106 L (3.0 bu) |
Key Specs - Seed Meters: |
Base MaxEmerge™ 5 vacuum Optional Radial bean Finger pickup Yes |
Lift System - Number of cylinders: |
1 |
Lift System - Type: |
Hydraulic frame lift |
Liquid Insecticide System - System available: |
No |
Markers - Control: |
Base Connected to planter lift Optional Independent of planter lift |
Markers - Less marker option: |
Yes |
Markers - Marker disk: |
Base 40.6 cm (16 in.) notched disk with depth gauging band |
Markers - Shear bolt protection: |
Yes |
Markers - Type: |
Folding |
Row Units - Adjustment: |
Handle |
Row Units - Depth gauging: |
2 solid or spoked gauge wheels |
Row Units - Opener: |
Tru-Vee™ Double Disk |
Row Units - Row unit down force: |
Non-adjustable (4 springs) No Adjustable heavy-duty Yes Pneumatic Yes |
Row Units - Row unit seed hoppers: |
Capacity Mini, 56 L (1.6 bu), 106 L (3.0 bu) Material Plastic |
Row Units - Scrapers, opener blades: |
Plastic rotary No Steel straight blade Yes Heavy-duty Yes |
Row Units - Seed tube sensors: |
Base AccuCount™ |
Row Units - Type: |
MaxEmerge™ 5 |
Row Units - Walking wheels: |
Yes |
Rows and Row Spacing - Number of rows: |
8 |
Rows and Row Spacing - Row spacing: |
76.2 cm (30 in.) |
Seed Meters - Base: |
MaxEmerge™ 5 vacuum |
Seed Meters - Central Commodity System: |
Seed capacity 1762 L (50 bu) |
Seed Meters - Finger pickup: |
Yes |
Seed Meters - Radial bean meter: |
Yes |
Seed Monitor System - Base: |
SeedStar™ 2 |
Seed Monitor System - Optional: |
ComputerTrak™ 350, SeedStar™ XP |
Tillage Attachments - .63-in. fluted blade (25 flutes): |
Yes |
Tillage Attachments - .7-in. fluted blade (13 flutes): |
Yes |
Tillage Attachments - Bubble blade: |
Yes |
Tillage Attachments - Row cleaner: |
Yes |
Tillage Attachments - Row cleaner - unit-mounted coulter: |
Yes |
Tillage Attachments - Unit-mounted coulter: |
Yes |
Tires - Base: |
VF445_50R22.5 implement (2 tires) 16x6.50-8 seed contact drive (1 tire) 16x6.50-8 fertilizer contact drive (1 tire) |
Tires - Quantity: |
2 |
Minimize compaction with large flotation tires
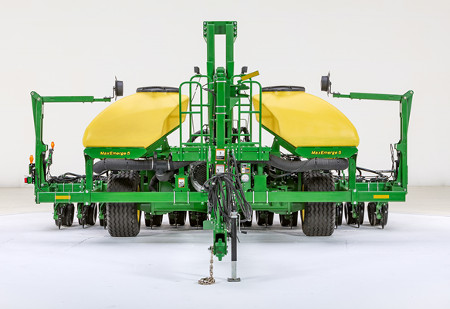
The 1745 Planter comes standard with radial flotation tires. Radial flotation tires can run at lower inflation pressures compared to bias tires. The lower inflation pressure allows the tire to squat, which increases the tire’s footprint and reduces the pressure applied to the ground.
- Two VF445/50R22.5 tread lightly
- Inflation pressure of 379.2 kPa (55 psi) when planter has a fertilizer system
- Inflation pressure of 310.3 kPa (45 psi) when planter has a Central Commodity System (CCS™) or is without fertilizer
Plant more ground between fills with the Central Commodity System (CCS™)
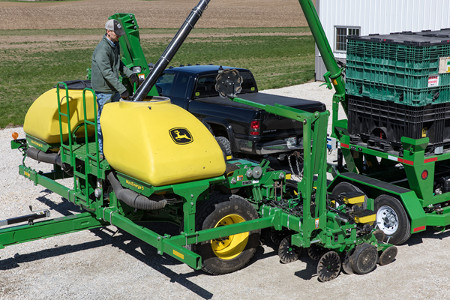
The CCS adds productivity through increased seed capacity, bulk fill capability, and easy, thorough cleanout.
- The two tanks have a combined capacity of 1,762 L (50 bu) which is 176 L (5 bu) more than a 15-row planter with 106-L (3-bu) hoppers.
- Translucent tanks allow the operator to see the seed level, and bin-level sensors alert the operator when the seed level is low.
- Filling the tanks is convenient due to a central filling location. The staircase and railing provide access to the filling platform between the tanks.
- Two platform lights improve visibility if filling at night.
- The following crops can be planted with CCS: corn, sweet corn, popcorn, cotton, sunflowers, sugar beets, soybeans, and sorghum (milo).
Cleanout is easy since a pro-box can fit under the CCS tanks when the planter is in the lifted position.
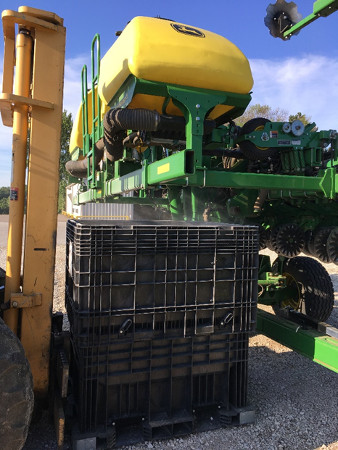
Increase versatility by applying liquid or dry fertilizer with a split-row planter
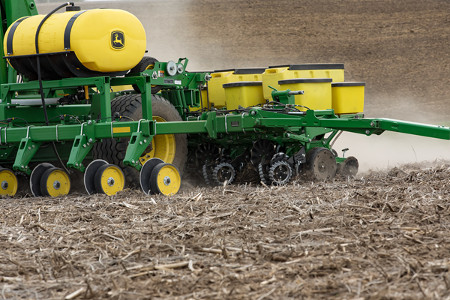
If you are looking to split-apply your fertilizer, the 1745 Planter offers liquid or dry fertilizer options on all non-bulk fill models, including split-row configurations.
- Liquid fertilizer with single-disk, frame-mounted offset openers or in-furrow placement is available with a storage capacity of 1,136 L (300 gal).
- Dry fertilizer with single-disk, frame-mounted offset openers is available with a storage capacity of 1,200 L (42.4 cu ft).
- Fertilizer application is on the front rank only, with 76.2-cm (30-in.) spacing.
- The fertilizer system is driven by a tire contact drive.
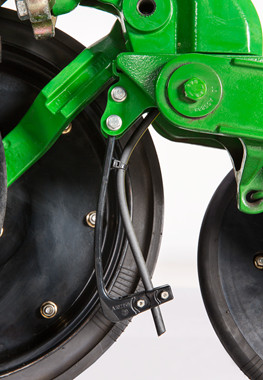
Compatibility with a wide range of tractors
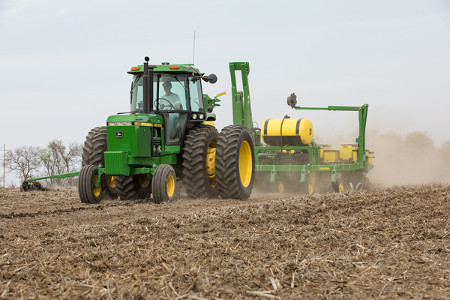
The simple design of the 1745 Planter makes it compatible with a wide range of tractors.
- Non-vacuum machine requires one selective control valve (SCV) when markers are tied to lift.
- Vacuum machine requires two SCVs when markers are tied to lift.
- There is a minimum drawbar horsepower requirement of 86.5 kW (116 hp) on a 15-row machine.
- There is a minimum drawbar horsepower requirement of 70.8 kW (95 hp) on an 8-row machine.
NOTE: Product features are based on published information at the time of publication and are subject to change without notice.
Save time by folding the planter from the cab
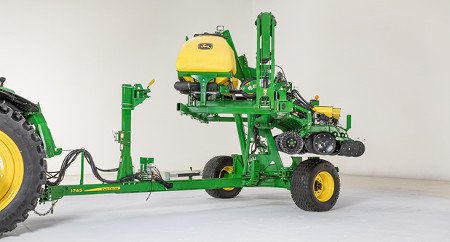
Minimize non-productive planting time by folding the planter from the cab of the tractor.
- Complete the unfold and fold cycles in less than one minute.
- By utilizing a frame control box, the base planter requires one selective control valve (SCV). Folding, raise/lower, and markers can all be tied to one hydraulic circuit.
John Deere Connected Support™ prevents downtime and efficiently resolves issues with revolutionary technology-based solutions
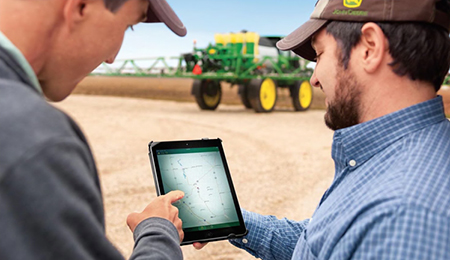
When you buy John Deere equipment, you expect reliability. You also know that problems can happen, and a product is only as good as the support behind it. That’s why John Deere equipment is prepared with technology that senses potential issues and can alert you and your dealer promptly—in the cab or anywhere you are.
John Deere Connected Support is a revolutionary change to support that leverages technology and the connectivity of JDLink™ telematics to prevent downtime and resolve problems faster. These tools decrease downtime by an average of 20 percent, enabling faster responses to unexpected problems and reducing technician trips to your machine. For some issues, unplanned downtime can even be prevented altogether through prediction of the issue.
With your permission, John Deere Connected Support:
- Keeps you running by monitoring machine health and promptly alerting you and your dealer of issues
- Saves time by remotely viewing in-cab displays, reducing trips to the machine
- Reduces or even eliminates technician trips to a machine through remote diagnostic and remote software reprogramming capabilities
- Connects experts with the information needed to respond to downtime faster and prevent it altogether
With more than a decade of experience leveraging connectivity to solve problems, no one else has the experience, tools, and knowledge to keep you running as John Deere and your John Deere dealer can. Connected Support is an in-base feature on all John Deere products with factory- or field-installed JDLink.
Reduce seed costs and increase corn yield potential with Section Control
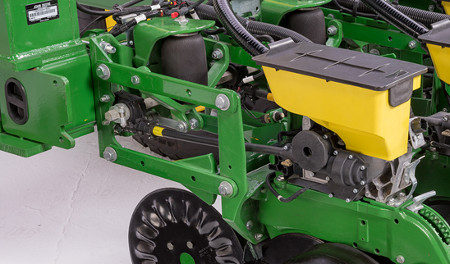

Section Control, in conjunction with the RowCommand feature on the planter, improves placement of seed, reduces yield penalties of over or under planting, and reduces operator fatigue. By automatically turning rows on and off, are fewer skips and overlap in the field. The automatic process allows the operator to focus on other aspects of planting, reducing overall stress and fatigue.
- University studies have shown seed savings of 1 to 12 percent, with an average of 4.3 percent.*
- In corn, the study found a 17 percent yield penalty in the double planted area.
- In corn, the study found a 757.6 L/ha (8.7 bu/acre) combine header loss in the double planted area.
- This leads to reduced operator stress and fatigue.
*NOTE: Runge, Max, et al. “Automatic section control technology for row crop planters.” Extension Alabama A&M & Auburn Universities ANR-2217, Oct. 2014. https://ssl.acesag.auburn.edu/pubs/docs/A/ANR-2217/ANR-2217-low-archive.pdf. Accessed 9 Oct. 2019
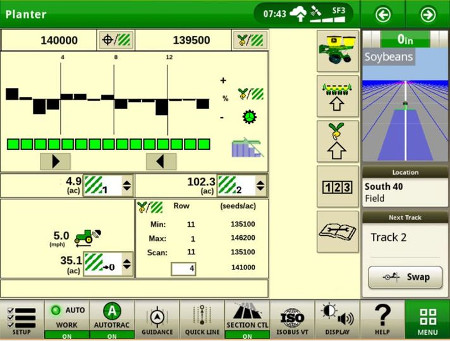
Field-proven and customizable MaxEmerge™ 5 row-unit
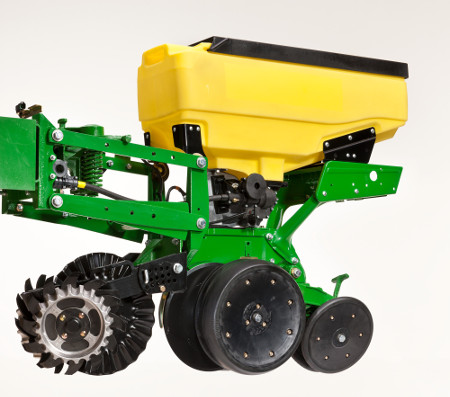
Introduced on model year 2015 planters, the MaxEmerge 5 row-unit is proven in the field. Using the same row-unit as ExactEmerge™ planters (less meter and BrushBelt™ delivery system), it was designed to withstand the stresses associated with high-speed operation. With an open side panel design, crop changeover on vacuum meters can be accomplished without removing the hopper from the row. The row-unit also provides you the versatility to match options to your operation.
- Choose finger pickup, radial bean, or vacuum meters
- Choose mini hoppers, 56-L (1.6-bu) hoppers, or 106-L (3.0-bu) hoppers
- Heavy-duty spring or pneumatic downforce
- Apply granular chemical with the insecticide option
- Variety of row cleaner and coulter options
- Spoked or smooth-sided gauge wheels
- Rubber or cast closing wheels
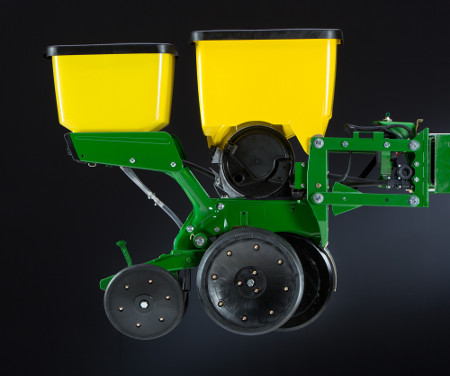
View planter performance with choice of three monitoring systems
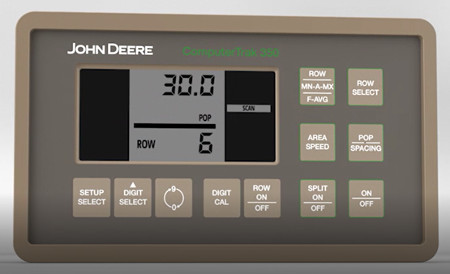
Your yield potential is never greater than when you take the seed out of the bag and put it in the ground. A lot can happen between the bag and the furrow, and that’s why John Deere offers three levels of planter monitoring systems, so you can choose what information you want to see in the cab.
- ComputerTrak 350 offers a base monitor that scans the rows to monitor population and spacing.
- SeedStar™ 2 provides a population monitoring bar graph to compare rows across the planter. It can also control the optional row shut-offs.
- SeedStar XP shows you population, seed singulation, seed spacing, downforce information, and ride quality. In addition, you can adjust the optional pneumatic down pressure and the optional row shut-offs from the display.
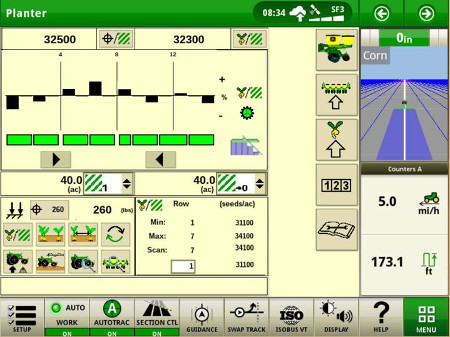
Maintain planting depth with choice of three downforce options
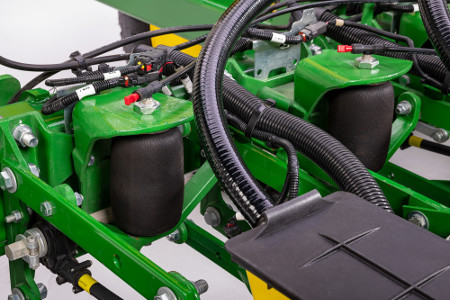
Overview
Planter row-unit downforce is an important factor to ensure consistent and proper depth control. With too little downforce, planter gauge wheels can lose ground contact and seeds will be planted at a shallow depth. This can result in uneven emergence, which studies have shown can impact yield 5 to 9 percent1. With too much downforce, furrow sidewalls can become smeared and compacted. Compacted sidewalls can result in hatchet roots, where plant roots grow parallel with the furrow but do not branch out between the rows.
Depending on the level of control the producer is looking for, the 1745 Planter offers three levels of downforce.
Adjustable heavy-duty downforce springs
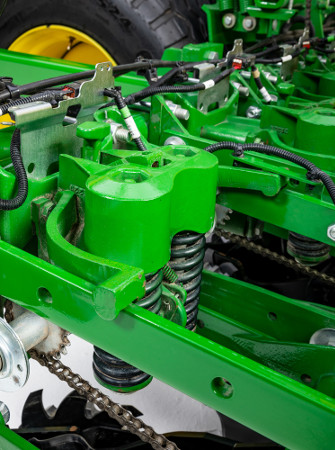
- Four downforce settings are manually adjusted for each row-unit.
- Rows behind tires can be set on a heavier setting.
- Downforce adjustments will take more time compared to pneumatic downforce systems.
Using set point pneumatic downforce
Watch the following video to better understand setting downforce by manually adjusting the pressure in the air bags.
SeedStar XP Operation and Adjustment – Using Set Point Pneumatic Downforce
1Doerge, T., Jeschke, M., and Carter, P. Planting outcome effects on corn yield. Crop Insights, Vol. 25, No. 1. DuPont Pioneer. https://www.deere.com/assets/publications/index.html?id=8557eeaf#1
Benefits
- Adjustable heavy-duty downforce springs provide four settings to match downforce requirements to field conditions: 0 kg (0 lb), 56.7 kg (125 lb), 113.4 kg (250 lb), and 181.4 kg (400 lb). Downforce is manually adjustable row-by-row.
- Manual control of pneumatic downforce provides simple adjustment of the whole planter from the electric compressor mounted on the front mast of the planter. The amount of downforce applied is infinitely adjustable from 6.8 to 181.4 kg (15 to 400 lb). Pneumatic downforce provides more consistent downforce throughout the range of row-unit travel compared to heavy duty downforce springs.
- Integrated control of pneumatic downforce provides simple adjustment of the whole planter conveniently from the tractor cab with the SeedStar™ XP monitoring system. Operators can see gauge wheel margin readings on three rows of the planter and either add or remove air from the pneumatic system to maintain a good level of load (margin) on the gauge wheels. The amount of downforce is infinitely adjustable from 6.8 to 181.4 kg (15 to 400 lb).
Pneumatic downforce system - Manual
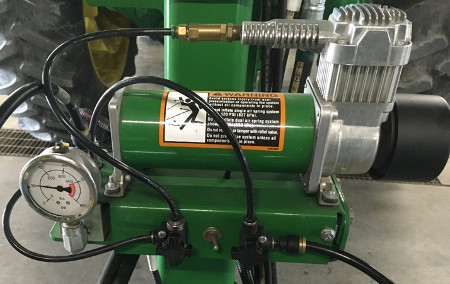
- Fill all the pneumatic air bags from one location on the planter.
- It includes simple on/off operation.
- The system has a valve stem which allows filling with shop air for faster fill times or for use as a backup if the compressor stops working.
- Split rows are plumbed on a separate circuit. This allows the air to be released only on the split rows when they need to be locked up for planting on 76.1-cm (30-in.) spacing. Set-point pressure is controlled for all rows when all rows are planting.
Pneumatic downforce system – Integrated
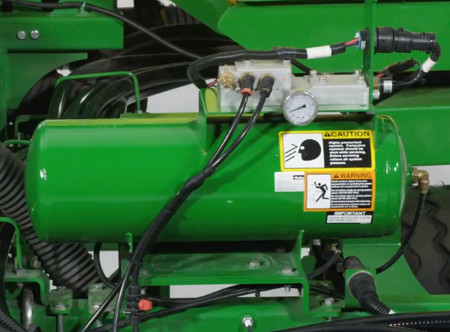
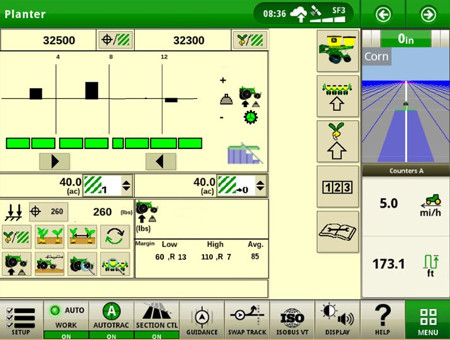
Understanding margin
Margin is the amount of weight riding on the gauge wheels to ensure proper planting depth and proper firming of furrow sidewalls. It can be calculated as follows:
Margin (A) = weight of row unit (B) + downforce applied (C) – resistance from the soil (D)
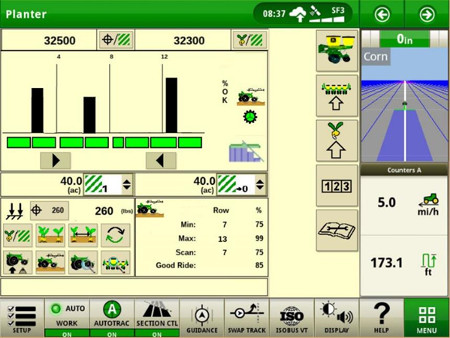
- Integrated downforce comes with an electric compressor and storage tank mounted on the rear of the planter for quick downforce adjustments.
- Downforce is easily adjusted from the display.
- The system has a valve stem which allows filling with shop air as a backup if the compressor stops working.
- The SeedStar XP monitor provides the operator downforce margin readings for the three rows equipped with a gauge wheel load sensor. Margin is essentially a reading of how much weight the gauge wheels are carrying. A positive margin ensures the planter is reaching correct planting depth. A target margin can be set to ensure proper firming of furrow sidewalls. Operators can add or remove air from the downforce system to meet the target margin.
- The SeedStar XP monitor provides the operator row-unit ride quality readings for the three rows equipped with the sensor node. Travel speed and field conditions can affect the amount of row-unit bounce that is experienced. Excessive row-unit bounce or vertical motion can cause problems with meter performance and spacing performance. The operator can slow down or increase downforce pressure to help the ride quality metric.
- Split rows are plumbed on a separate circuit. This allows the air to be released only on the split rows when they need to be locked up for planting on 76.1-cm (30-in.) spacing. Set-point pressure is controlled for all rows when all rows are planting.
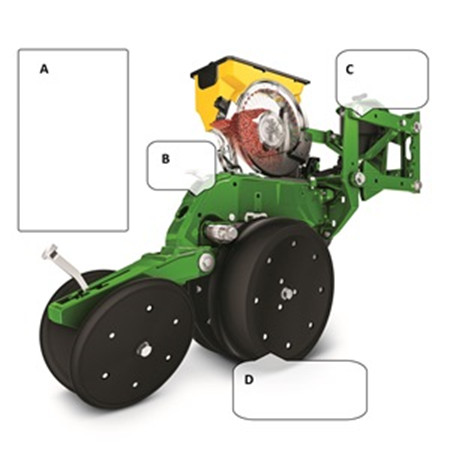
An example could be as follows:
- A – Margin: 45.4 kg (100 lb)
- B – Weight of row-unit: 54.4 kg (120 lb)
- C – Downforce applied: 59 kg (130 lb)
- D – Soil resistance: 68 kg (150 lb)
- A=B+C-D
- 4 kg (100 lb) of margin = 54.4 kg (120 lb) + 59 kg (130 lb) – 68 kg (150 lb)
Soil resistance will vary based on planting speed, planting depth, soil type, and row-unit attachments such as closing wheel pressure setting, coulter setting, and row cleaner setting.
Watch the following video to better understand margin and how to set the correct margin for field conditions.
Maximize productivity with two planter configurations to match your operation
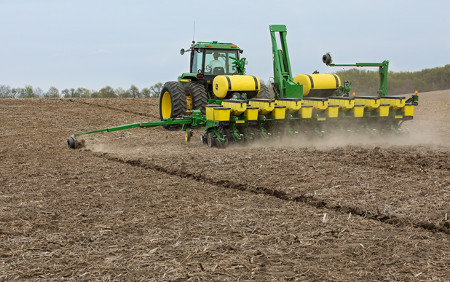
The 1745 Planter comes in two main row-unit configurations with the option of keeping it simple or adding more advanced features.
- 8-row, 76.2-cm (30-in.) configuration
- 15-row, 38.1-cm (15-in.) configuration allows for planting corn in 76.2-cm (30-in.) rows and soybeans in 38.1-cm (15-in.) rows
- Select between mechanical or vacuum meters.
- Dry or liquid fertilizer is available on all non-Central Commodity System (CCS™) models.
- Select more advanced options like the Pro-Shaft™ cable drive system, RowCommand™ row clutches, CCS, and the SeedStar™ XP monitoring system.
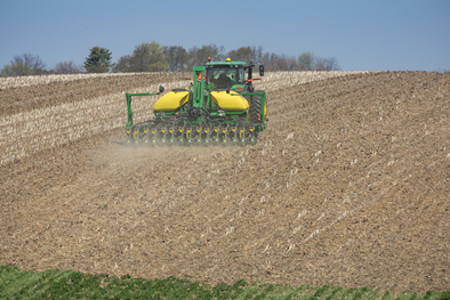
Easily navigate roads with narrow transport position
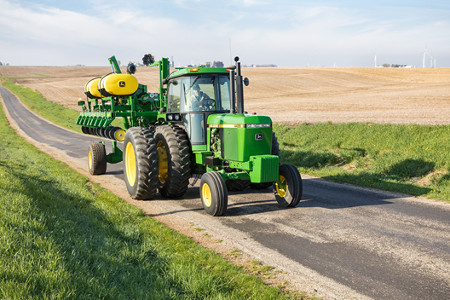
Navigate narrow roads, bridges, and field entrances with the narrow transport position of the 1745 Planter.
- Planter follows the standard duals on a tractor
- Typical transport width of 3.71 m (12 ft, 2 in.)*
- Typical transport height of 3.84 m (12 ft, 7 in.)*
- Main hydraulic cylinder mast can be lowered under 3.68 m (12 ft) for storage
- Row-units fold toward the center of the road for stability
- Comparable non-folding 1785 Planter has a typical transport width of 6.96 m (22 ft, 10 in.).
*NOTE: Transport dimensions may vary based on options. Product features are based on published information at the time of publication and are subject to change without notice.